Imagine knowing exactly where and when your aircraft, pipeline, wind turbine, or ship will start to corrode. That’s the promise of digital twin technology, and it is one of the fast-evolving technologies for asset monitoring.
A digital twin is a virtual replica of an object or system that continuously mirrors its real-world counterpart using data from sensors, inspections, and environmental monitoring. The application in corrosion prediction is compelling because corrosion is both predictable and costly, causing an estimated $2.5 trillion in global economic losses annually¹.
In the corrosion world, digital twins work by combining environmental measurements of temperature, humidity, and chemical contaminants with sophisticated models that simulate how these conditions affect different materials over time. Acuity Corrosion Technology from Luna Labs USA uses this approach, deploying battery-powered sensors on aircraft, ships, or industrial equipment to continuously track corrosivity in real-time. These physical sensors feed data to machine learning algorithms that can also create “virtual sensors” for hard-to-reach locations, essentially allowing engineers to monitor corrosion risk across an entire asset even when they can only place physical sensors in easily accessible spots.
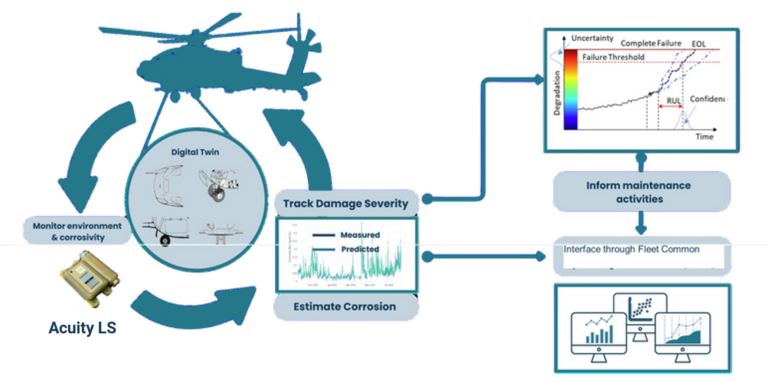
The real breakthrough comes from moving beyond traditional time-based maintenance schedules to condition-based strategies. Instead of inspecting an aircraft regardless of its actual condition and history, digital twins can predict when an aircraft or zone within an aircraft will need attention. This precision dramatically reduces unnecessary maintenance costs while informing preventative maintenance and reducing costly unscheduled maintenance and repairs.
Collaboration between Acuity and BEASY Innovative Solutions, a leading corrosion predictive modeling company, demonstrates how this technology is evolving beyond simple monitoring to comprehensive predictive modeling. By combining Acuity’s environmental sensing capabilities with BEASY’s advanced electrochemical and corrosion modeling (PolCurveX and Corrosion Manager), the team is creating digital twins that can predict not just when corrosion will occur, but exactly where it will be most severe. This integrated approach enables engineers to optimize material selection during design, improve protective coating strategies, and schedule maintenance with more precision.
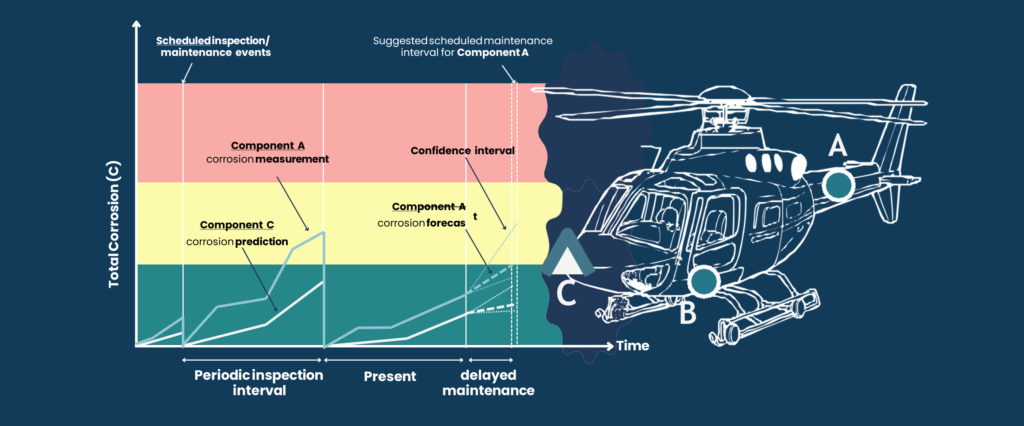
The future of corrosion management is about preventing corrosion through intelligent prediction. As digital twin technology continues to mature, the ability to forecast when an asset needs attention will transform corrosion maintenance into a strategic cost- and time saving initiative.
1. NACE 2016 Impact Report. International Measures of Prevention, Application, and Economics of Corrosion Technology (IMPACT) Study. impact.nace.org
Contact our corrosion team to discuss digital twin and other Acuity solutions.