Members of our Acuity corrosion team recently presented work at the 2024 AMPP Annual Conference and Expo. We had several opportunities to share the advances we are making to understand and address corrosion mitigation and prevention.
Real-time Measurement of Aerospace Organic Coating Condition and Performance in Atmospheric Corrosion Conditions
Key words: galvanic corrosion, atmospheric corrosion, coating degradation, electrochemical measurements, corrosion modeling
Working with collaborators from the Georgia Institute of Technology Industrial and Systems Engineering, our team has developed a novel statistical modeling framework to measure protective coating health and predict coating failure. Using real-time electrochemical monitoring, visual inspection during laboratory testing, and outdoor testing measurements, the study identified two types of discrete events leading to coating failure: a corrosion-current-based event and an environmental condition-based event. Coating failure predictions during laboratory testing provided failure prediction windows that were applicable to a range of aerospace coating types (chromate, non-chromate, waterborne, and solvent borne).
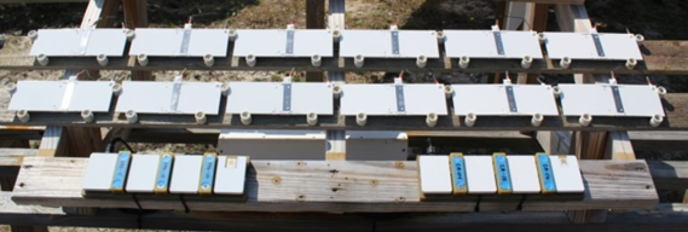
Chromate and non-chromate samples: 6-month outdoor exposure on multi-sensor Acuity panels
The results demonstrate the ability of the stochastic model to detect loss of inhibitor protection and predict coating failure in comparison to observational results. The Acuity™ monitoring systems used to make these measurements for aerospace coatings are commercially available from Luna Labs and the test methods are detailed in AMPP TM21449-2021.
This material is based upon work supported by the SERDP Program under WP19-1168.
Real-Time Measurement of Electrocoat, Powder Coat, and Organic Coatings for Atmospheric Galvanic Corrosion Protection
Key words: galvanic corrosion, coating degradation, electrochemical measurements, electrocoat, power coat, lap joint sample
Although powder coat and electrocoat (E-coat) finishes are commonly used in the automotive industry, these coatings have found limited use in aerospace applications. For improved understanding of the performance of these coatings to protect galvanically coupled aerospace materials, a measurement system was developed and adapted to automotive samples for aerospace testing. A real-time measurement system was developed to evaluate coating performance of liquid spray coatings, e-coat, and powder coatings. The results demonstrate the ability of this system to obtain continuous measurements of galvanic corrosion for multiple samples in a variety of accelerated laboratory tests. These measurement techniques demonstrated the ability to use lap joint samples to evaluate the corrosion at crevices and quantify the protective properties of a number of coating systems to protect a range of materials relevant to both aerospace and automotive applications.
This material is based upon work supported the United States Air Force AFRL/SBRK under contract FA864921P1498.
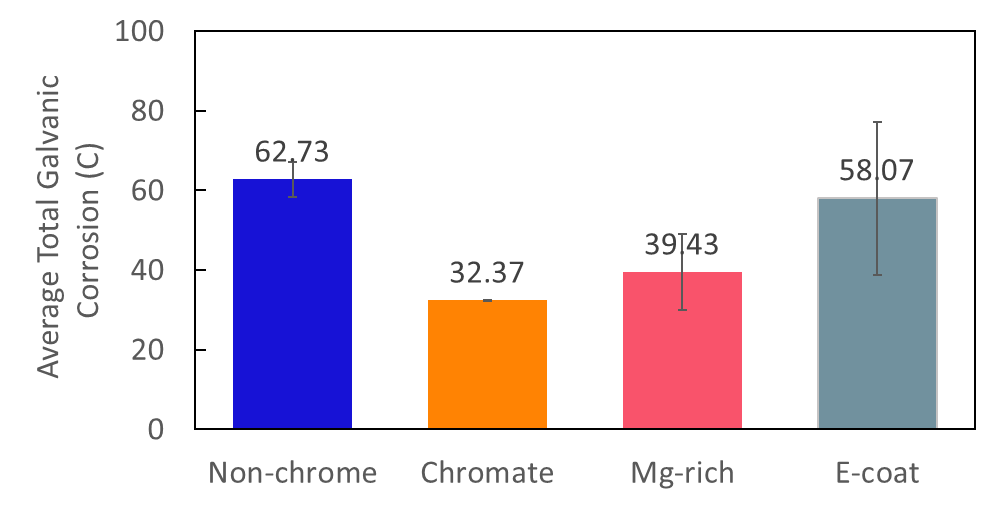
The measurement system can differentiate between coatings including traditional aerospace coatings.
Leveraging Physical and Virtual On-Aircraft Sensors to Inform Maintenance Practices
Key words: galvanic corrosion, corrosion sensor, machine learning, CBM+, aircraft maintenance
Working with collaborators at QTEC Aerospace, Lockheed Martin, Sikorsky, and the University of Dayton Research Institute, our team created a set of models for tiered severity predictions, allowing flexibility of the predictions based on available information. The current work was focused on predicting hourly corrosion rates from environmental parameters, independent of the location, and was demonstrated to be robust when applied to locations and timeframes outside of the training dataset.
The validation provided in this work is another step toward applying these models to track individual asset severity, based on flight records, within a digital twin software application. A key finding from this work highlighted that local environment measurements from sensing devices inform the best performing model, but that nearby weather stations (i.e., publicly available measurements) can inform a well performing model, if the data are correctly preprocessed. Although sensing devices can provide more spatially-resolved predictions from local environment variations, either model can be used to accurately predict hourly corrosion rates, based on the available information.
Predicted corrosion rates and severity can directly be correlated to corrosion-related maintenance manhours for a given asset, enabling better informed long-term maintenance schedules, and planning to reduce costs and improve asset availability.
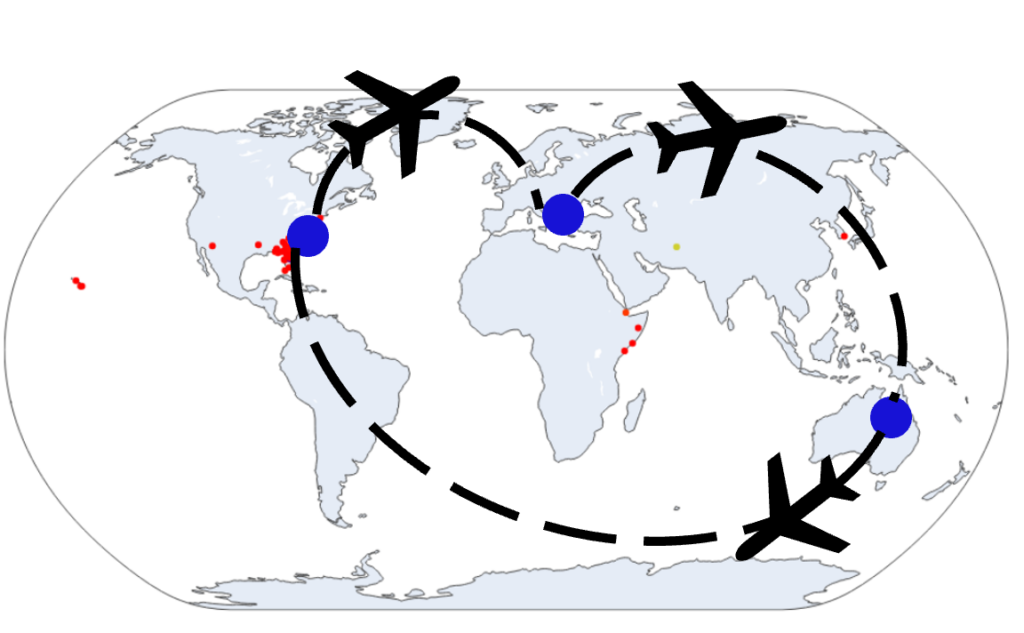
Dynamic environmental and corrosion severity monitoring based on flight records, weather information, and local on-asset sensing devices.
Electrochemical Sensors for Atmospheric Corrosion Monitoring and Materials Testing
Key words: electrochemical measurements, atmospheric corrosion, corrosion monitoring system, coatings performance, asset tracking systems, environment spectra
The Acuity corrosion team developed monitoring systems and support the standardization of environment severity and atmospheric corrosion measurements that utilized two-electrode electrochemical sensors. Published as ISO 22858:2020 Corrosion of metals and alloys – electrochemical measurements – Test method for monitoring atmospheric corrosion, the electrochemical sensors and monitoring systems provide continuous environment and corrosion measurements, including humidity, temperature, contaminant/salt loading, and corrosion rates, for severity assessment, materials characterization, and asset management.
The method describes sensors and measurements that are useful for continuous monitoring of environment conditions and corrosion in laboratory tests, outdoor exposures, and on assets. Site severity can be assessed using multiple environment and corrosion parameters; while, alloy corrosion and coating protection can be quantified continuously throughout a test or exposure.
The small size, durability, and reliability of the Acuity LS™ device make it useful for asset monitoring, adding a new dimension to condition based maintenance of mobile and fixed assets.
Find out more about Acuity Corrosion Technology at https://bit.ly/3WkFBtd.
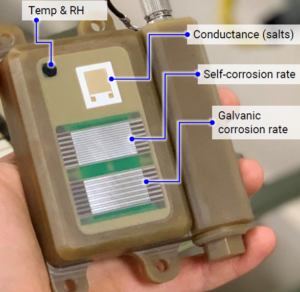
Acuity Corrosion Technology: Autonomous, battery powered devices that perform periodic measurements, data storage over long time periods.
Contact our corrosion team to discuss these and other ongoing research initiatives.