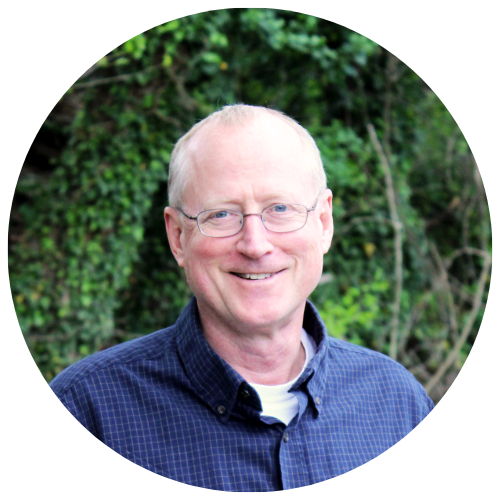
The 24th SURFAIR Congress in Biarritz, France was the perfect opportunity to share valuable information about advances made by our corrosion teams with the goal of protecting structures against corrosion.
One of the premier international conferences addressing finishes and processing in the aerospace industry, the focus this year is on, in part, performance, durability, and sustainability – areas where our corrosion products and expertise shine.
Blockade GC: A non-chrome and non-hazardous galvanic corrosion protective coating
Adam Goff, Materials Fellow and Team Lead at Luna Labs, presented on Blockade GCTM, a non-chrome and non-hazardous corrosion control coating for fasteners and other galvanic interfaces. Galvanic corrosion between aluminum and other dissimilar metals (e.g. fasteners) represents a significant portion of total maintenance costs and upkeep for aircraft. There is a need for environmentally friendly protective coatings that are easy to apply and implement that offer next-generation protection.
Blockade GC functions by preventing galvanic coupling between components, hindering corrosion development, increasing durability, and improving overall performance. This eco-friendly, cost-effective coating can be factory applied or by a qualified applicator, allowing for direct installation of parts without extra steps. Blockade GC can uniquely enable a fully non-chrome material stackup where other non-chrome materials have failed. It can be used in numerous aircraft applications ranging from screws, bushings, rivets and many other dissimilar metallic interfaces
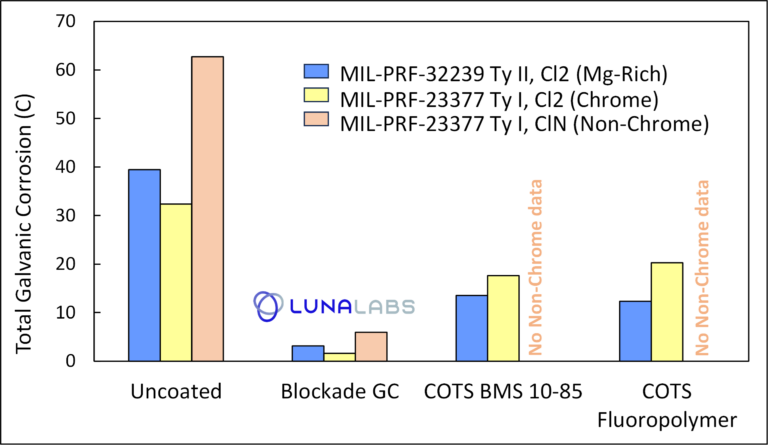
Total accumulated galvanic corrosion for 7075-T6 coupons as a function of exposure time for three different primer systems with uncoated, BMS 10-85, COTS Fluoropolymer, or Blockade GC coated and mated 316SS coupons. Blockade GC resulted in the lowest total galvanic corrosion for all primer types.
Acuity Corrosion Technology: Bringing data-driven insights to corrosion management
Committee member, Fritz Friedersdorf, presented the results of a multi-year collaborative research effort with Georgia Tech, the Southwest Research Institute, and The Boeing Company to develop test methods and establish models for the degradation of aerospace coatings. These methods and models will reduce the risk of new coating introductions for chromate elimination. Processes specific to aerospace applications have been addressed including coating cracking at structural discontinuities and protection from galvanic corrosion measured with Acuity LS devices in laboratory, outdoor, and on-aircraft evaluations.
The coating performance and loss of corrosion protection is associated inhibitor chemistry, leaching, and inhibitor concentration at a coating defect. High severity events are potentially more important in coating failure as compared to time in service, and a temporal point process model was determined to be the most suitable for predicting coating degradation and corrosion protection.
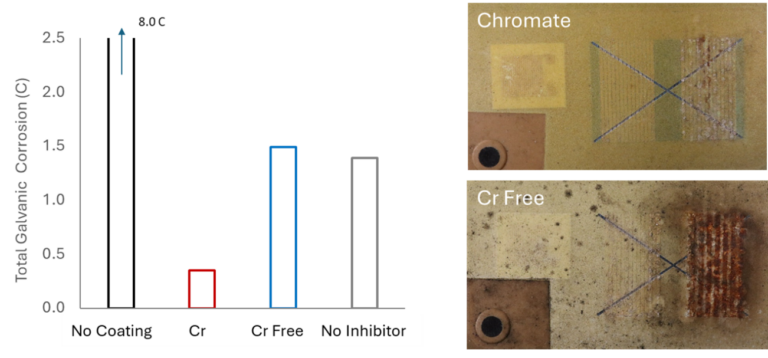
Total aluminum versus stainless steel galvanic corrosion for multiple coating systems tested for 1.5 months at a marine exposure site (left). Images of coated and scribed sensors after testing (right).
Luna Labs Corrosion Resources
Questions or need more info? Let us know.